Literal Lean -
When Lean Meets Sustainability
As a Lean Six Sigma Master Blackbelt and Product Manager at Envetec Sustainable Technologies something has been niggling at me: why isn’t “waste” itself categorized as one of the 7 Wastes in Lean methodology?
At first glance, it may sound a bit unconventional. However, consider how the concept of “waste” has evolved. In some circles, the traditional seven wastes of Lean are being expanded to include an eighth waste—unused talent. When that idea was introduced, people likely thought, “Yeah, that makes sense; how did we not think of that before?”
With that in mind, should we not reevaluate our approach to waste itself, especially in industries where single-use materials are unavoidable, such as healthcare and medical waste treatment?
Lean in Everyday Life
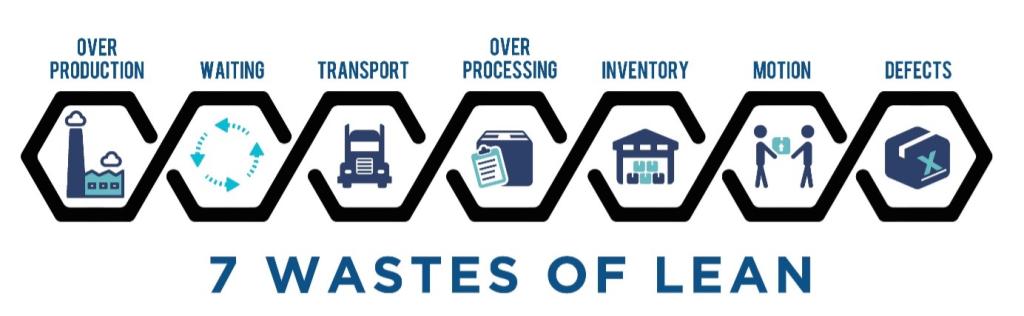
(Source: https://gembaconcepts.com/blog/timwood-a-tree-to-cut/)
Lean principles have been applied across industries for over a century, even before being formally recognized as Lean. In fact, we unknowingly apply Lean principles in our everyday lives.
- Why is your toaster placed near the cutlery drawer? It reduces motion when preparing toast.
- Why do airport escalators get more traffic than elevators? Continuous flow is preferred over batch processes.
- Why make a grocery list instead of randomly purchasing items? To minimize inventory waste.
Lean is all around us, we just have to know what to look for.
The concept of Lean gained prominence when Toyota introduced its production model in the 1980s. The methodology has evolved over the years, but its core values remain the same: eliminating waste and adding customer value through continuous improvement.
Continuous Improvement and the Circular Economy
In the spirit of Lean’s core values— eliminating waste and adding customer value through continuous improvement—Envetec developed GENERATIONS®, which takes biohazardous waste from laboratories, including all commonly used polymers, treats material using a non-thermal process involving simultaneous shredding and chemical disinfection, and produces a flake-like end product that is suitable for biohazardous waste recycling. This process not only keeps waste out of landfills but also reintroduces it into the economy, creating new possibilities for what was once considered waste.
This prompts a crucial question: When does waste actually become waste?
With technologies such as GENERATIONS, waste may not be waste at all—it can become a valuable feedstock waiting for the right technology.
Rethinking the Value of Waste
Many people are aware of the proverb, “One man’s trash is another man’s treasure,” and nowhere is this truer than in Envetec’s approach to biohazardous waste recycling. GENERATIONS is driving positive change across multiple industries, proving that what was once considered waste can be reused and reintegrated into the economy.
But how often do we discard something and believe it has no further use? How often do we overlook the potential for waste to add value?
Hence, “Literal Lean” emerged—a concept borne from a Lean mindset and brought to life by a technology dedicated to eliminating the cradle-to-grave mentality. Literal Lean represents the repurposing of physical waste back into the economy, adding customer value and fostering environmental stewardship through innovative medical waste treatment practices.
Earlier, I mentioned that we often don’t even realize we are using Lean, so let’s take a closer look at GENERATIONS. Applying Literal Lean methodology, our technology is adding value far beyond eliminating physical waste.
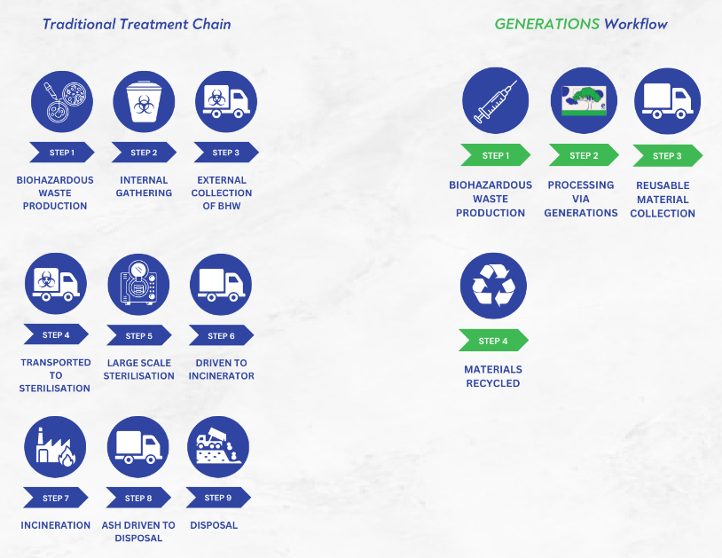
Take the two process flows above: the one on the left is the conventional flow of biohazardous waste disposal and the one on the right is the GENERATIONS process commonly seen with medical waste treatment, showing how clinical waste collection and recycling is a much more efficient process.
- The GENERATIONS flow eliminates three transport waste steps.
- The GENERATIONS flow eliminates two over-processing waste steps.
- The GENERATIONS flow eliminates one waiting waste step—the plastics to degrade—a considerable waiting period given that the average time for the plastic to degrade is 1,000 years.
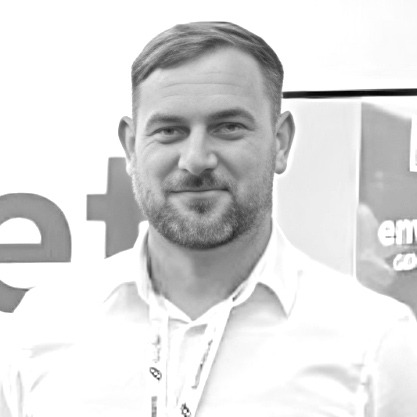
As I mentioned, we sometimes use Lean without even realizing it. The GENERATIONS system has eliminated seven wasteful steps, including the waste itself.
Does it still sound crazy or are we crazy not to give it a chance?